How Can Quality Circles Help Your Company?
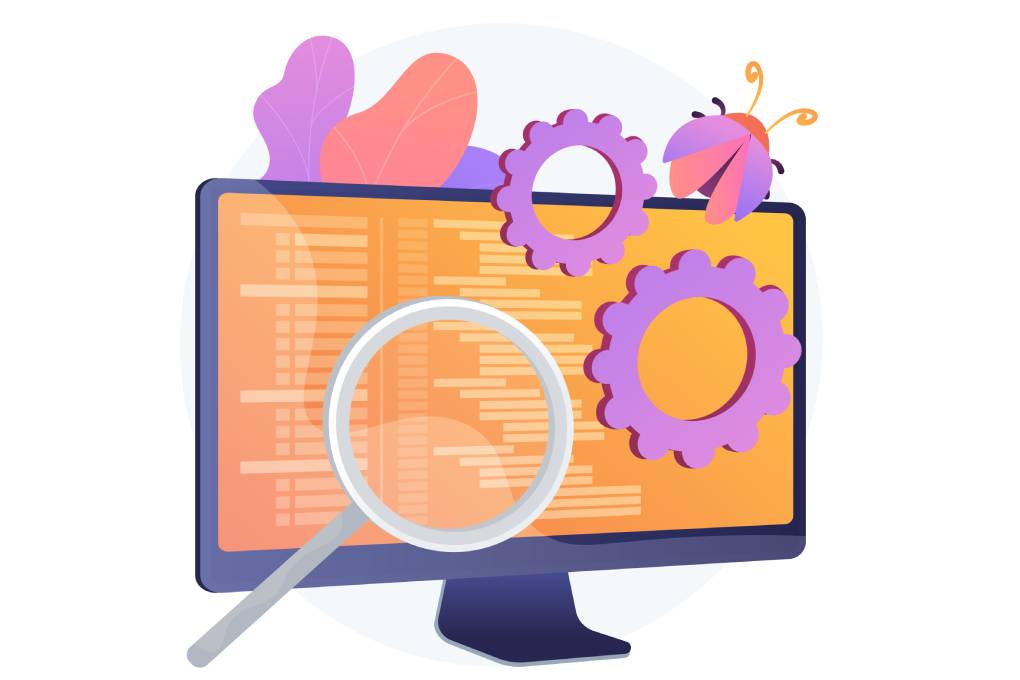
The Quality Circles are one of the new elements heard in the field of Human Resources. Their advantages to improve the performance of the company and the employee experience have made them a new element to consider.
Composed of between 4 and 8 workers, it is a unique option for medium and large companies to make their workers participate in the same decisions, directly affecting their work and working conditions.
Although a lot has been written about quality circles in recent years, we will try to shed light on their operation, implementation, monitoring, and the most exciting topics to deal with, and which ones should not be covered with this system.
Table of Contents
What Is A Quality Circle?
The quality circle concept was born in Japan at the end of the 20th century. Specifically, its inventor was Kaoru Ishikawa, the creator of the Ishikawa diagram.
This Japanese chemist developed at the end of the 60s a whole theory about the efficiency of Japanese companies over Western ones, explaining and designing the quality circle for the first time.
How To Implement A Quality Circle?
Although in the first theory of these circles, it was an element born spontaneously in the company, today it is clear that the management must know the concept and promote it.
In addition, to facilitate its operation, a facilitator is proposed in each group. A facilitator is a person who coordinates and directs the meetings at first, although it is a role that can rotate between the different members of the circle.
At first, especially in companies with more resources, the facilitator can be an external person with experience in quality circles, team work methodologies, etc … who will pass on their knowledge until their work is not necessary.
Likewise, the same circles can vary from member to member or become transversal between members of various departments, the most common in small and medium-sized companies.
The Quality Circle Creation Process
To clarify the operation process of one of these circles, these are the ten steps to follow:
- The decision by the management of the company.
- Hire/appoint and train facilitators.
- Creation of a support structure for the circles.
- Design or choice of methodology for quality circles.
- Creation of the quality circle.
- Institutional declaration of support for the circle.
- Selection of topics according to priority.
- I work on the selected topics.
- Elaboration of quality improvement programs.
- Presentation of results reports to superiors.
Follow Up
The monitoring of the results of the quality circle is as important as the establishment of the circle itself. If the solutions are proposed, we forget about them, and the company will not advance and improve. The effort (and the hours spent) will have been worthless, and employees may feel frustrated and unmotivated.
For follow-up, the first step is for the report to reach the competent superior in each case. In some cases, it will be the department head himself who can take charge of the situation. In others, you will have to be referred to the company’s CEO. It is advisable to approve the new proposals as quickly as possible, achieving an internal process of continuous improvement.
In a short time, the results should be evaluated. If these results are not as expected, it will be necessary to see if some corrective can be applied to save the situation. If it is not possible to establish such corrections, it will be necessary to cancel the improvement and redefine the processes of the circle so that it works the next time.
As with any business decision, success is not always achieved, although being direct proposals from the people in charge of a job, the most common is that they end up working. Either way, you have to be patient and keep relying on employee input. Maybe the next one is the upgrade the company has been waiting for.
Also Read: When Work Becomes A Passion